Kursarbeit: Beschreibung des Designs und Zwecks des Teils, Analyse seiner Herstellbarkeit. Allgemeine Empfehlungen zum Erstellen von Bildern und Zeichnungsmaßen für eine Teilezeichnung. Berechnung der erforderlichen Spannkraft des Werkstücks
MOSKAUER AUTOMOBIL- UND STRASSENINSTITUT (STAATLICHE TECHNISCHE UNIVERSITÄT)
O.A.OGANESOV, N.N.KUZENEVA
INFORMATION
MATERIAL
LERNPROGRAMM
MOSKAU 2008
UDC 744:621:72 BBK 30,11:34,4:38,712
Oganesov O.A., Kuzeneva N.N. Technische Grafiken. Referenzmaterialien: Lehrbuch/MADI(GTU). Teil 3. -M., 2008. -93p.
Gutachter: Ph.D. Technik. Wissenschaften, Professor O.V. Georgievsky (MGSU), Ph.D. Technik. Naturwissenschaften, außerordentlicher Professor P.R. Dobrogaev MADI (GTU).
Im letzten dritten Teil Lehrhilfe beschreibt die allgemeinen Regeln für die Erstellung von Teilezeichnungen, einschließlich ihrer Skizzen, und Zeichnungen von Baugruppen und gibt außerdem Empfehlungen für die Detaillierung der Zeichnung Gesamtansicht, einschließlich des Lesens. Das Handbuch enthält Arbeitszeichnungen von Teilen, die häufig in Maschinenkonstruktionen verwendet werden, mit Standardbildern und Originalteilen.
Das Lehrbuch richtet sich an MADI-Studenten (GTU) im ersten bis zweiten Studienjahr, die technische Grafik studieren, und kann für ältere Maschinenbaustudenten bei der Durchführung nützlich sein Kursarbeit und Projekte.
© Moskauer Institut für Automobil- und Straßenwesen (Staatliche Technische Universität), 2008
12. DETAILZEICHNUNGEN
12.1. Arten von Produkten und Designdokumenten
Ein Produkt ist ein beliebiger Artikel oder eine Gruppe von Artikeln, die hergestellt werden sollen. Im Schulungskurs technische Grafiken Von den Produkten werden nur Teile und Baugruppen berücksichtigt.
Ein Teil ist ein nicht spezifiziertes Produkt, das aus einem homogenen Material besteht und keine Komponenten aufweist, die durch Montagevorgänge verbunden werden müssen.
Montageeinheit- ein bestimmtes Produkt, dessen Bestandteile durch Montagevorgänge – Schrauben, Schweißen, Löten, Nieten, Bördeln usw. – miteinander verbunden werden.
Die Zusammensetzung und das Design des Produkts werden durch die in GOST 2.102-68* festgelegten Designdokumente bestimmt. Wird in Bildungseinrichtungen verwendet Trainingszeichnungen - Teilezeichnungen, Montagezeichnungen, Übersichtszeichnungen und Spezifikationen, die sich geringfügig von den Prunterscheiden.
12.2. Teilezeichnung und Grundvoraussetzungen dafür
Zeichnungs-(Arbeits-)Details - Haupt Entwurfsdokument, mit Bildern des Teils und anderen Daten, die für seine Herstellung und Kontrolle erforderlich sind. Die Qualität des Teils hängt von seiner korrekten Ausführung ab.
Das Teil in der Zeichnung ist in seiner fertigen Form mit den Formen und Abmessungen dargestellt, die es vor dem Zusammenbau haben sollte.
Teilezeichnungen werden je nach Zweck und Ausführungsart in Skizzen (siehe 12.7) und tatsächliche Teilezeichnungen unterteilt, auf die weiter eingegangen wird.
Die Tutorial-Zeichnung des Teils enthält Bilder und Abmessungen des Teils., die seine Form vollständig widerspiegelt, sowie
Informationen zu Name und Material des Teils, Maßstab, Anzahl der Zeichnungsblätter, sein Testamentsvollstrecker und der Lehrer, der die Zeichnung entgegennimmt, im Titelblock angegeben. Die Zeichnung kann Beschriftungen enthalten, die die Bilder des Teils mit Informationen zu dessen Parametern, Material, individuellen Abmessungen usw. ergänzen.
Eine Übungszeichnung eines Details wird auf einem Blatt Whatman-Papier mit einem Zeichenwerkzeug im Standardmaßstab erstellt und gemäß den Standards für Formate, Linien, Schriftarten usw. erstellt.
Das Hauptkriterium für die Bewertung einer Zeichnung ist ihre Benutzerfreundlichkeit., abhängig von der Anzahl der Bilder des Produkts, ihre gegenseitige
Standort, Größe, Maßstab usw.
ZU Die Anzahl der Bilder und Abmessungen in der Zeichnung sollte minimal sein, aber ausreichend für die vollständige Offenlegung externer und innere Formen Details und Gewährleistung der Reversibilität der Zeichnung. Es ist zulässig, mehr als die Mindestanzahl an Bildern bereitzustellen, wenn dies die Lesbarkeit der Zeichnung erheblich erleichtert. Allgemeine Regeln Das Erstellen von Bildern von Teilen und das Zeichnen von Abmessungen auf der Zeichnung wird von GOST festgelegt 2.305-68* und GOST 2.307-68*.
Bei der Auswahl einer Skala Zeichnungen berücksichtigen die Komplexität der Form des Teils, seine tatsächlichen Abmessungen und das Verhältnis zwischen den Größen der einzelnen Elemente des Teils.
Im Schulungskurs werden alle Zeichnungen auf einem Blatt erstellt, daher ist in der Spalte „Blätter“ der Hauptbeschriftung „1“ angegeben.
Zeichenpapiergröße Die Auswahl erfolgt unter Berücksichtigung der Anzahl der Bilder, ihres Layouts, ihres Maßstabs und ihrer einfachen Größenanpassung. Es wird empfohlen, dass Bilder nach Möglichkeit 40–50 % und Bilder und Abmessungen 70–80 % der Blattfläche einnehmen.
Übungszeichnungen von Teilen werden anhand des fertigen Teils erstellt.,nach einer Skizze eines Teils oder einer Gesamtansichtszeichnung einer Baugruppe, bei dem das Teil ein integraler Bestandteil des Produkts ist.
12.3. Teilegruppen Es gibt drei Gruppen von Teilen:
1. Standardteile, gekennzeichnet durch praktische Formen und eine große Auswahl an Größen (Bolzen, Muttern, Dübel usw.). Arbeitszeichnungen dieser Teile sind in den einschlägigen Normen enthalten, die die Form des Teils, seine Abbildungen in der Zeichnung, Abmessungen und Regeln für ihre Anwendung regeln.
2. Teile mit Standardbildern:
- Teile, deren Bilder vollständig durch Normen geregelt sind (Federn), und Teile, die die Form von Normteilen haben, sich jedoch in mehreren Größen von diesen unterscheiden. Bilder und Regeln für die Dimensionierung dieser Teile sind durch Standards festgelegt, die Größenwerte jedoch nicht;
- Teile, deren Hauptelemente Standardbilder, Größen und Regeln für ihre Anwendung haben (Teile mit Getriebeelementen, Rohrleitungen usw.);
- Teile aus Sorten- und Plattenmaterial mit teilweise regulierten Bildern und Abmessungen.
3. Originalteile, deren Form ganz oder teilweise von der Form von Standardteilen abweicht und mit Standardbildern.
Dementsprechend werden Teilezeichnungen in Zeichnungen von Normteilen mit Standardbildern und Originalzeichnungen unterteilt.
12.4. Arten von Teilen und ihre Elemente
Teile werden nach Design und technologischen Merkmalen unterschieden.
Designteiltyphängt von seinem Zweck und seinen betrieblichen Funktionen ab.Technologische Art des Teils(gegossen, gestanzt usw.) bestimmt die Art seiner Hauptbearbeitung, die der Form des Teils besondere charakteristische Merkmale verleiht.
Jeder Teil ist eine bestimmte Menge von Elementen, die zu einem Ganzen zusammengefasst sind.
Ein Element eines Teils ist ein separater Teil davon, der seinen eigenen Zweck hat (Löcher, Nuten, Abflachungen, Gewinde usw. – siehe Abb. 12.1).
Je nach Zweck werden die Elemente eines Teils in strukturelle, technologische und informative Elemente unterteilt.
(Slot)
Nut (Nut)
Rille
Nutloch Blinddurchgangsloch
Loch
Center
Nut (Nut, | ||||
Geschlüsselt | ||||
Steifigkeit
Loch
Galtel Galtel
Pfotenflut
Strukturelemente (Zahnräder, Keilnuten usw.) stellen sicher, dass das Teil seine betrieblichen Funktionen und Eigenschaften erfüllt und zu einem bestimmten Konstruktionstyp gehört.
Technologische Elementesorgen für eine einfache Herstellung des Teils (Unterstützung des Teils während der Bearbeitung) und seine Montage mit anderen Teilen (Fasen, Nuten) oder hängen mit den Herstellungsmerkmalen des Teils (Gusskehlen und -schrägen für Gussteile) und seiner Elemente (Läufe und) zusammen Hinterschnitte von Gewinden, Nuten etc. .). Technologische Elemente in Schulungszeichnungen werden manchmal nicht vereinfacht oder konventionell dargestellt oder dargestellt.
Informationselemente(Schilder, Beschriftungen, Indizes) werden normalerweise in Form von Vorsprüngen und Vertiefungen auf den Oberflächen des Teils angebracht und auf der Zeichnung genau dargestellt.
Die Form eines Teilelements hängt von den Funktionen ab, die es ausführt. Unterscheiden einfache Elemente gebildet durch eine Oberfläche und komplex, gebildet durch zwei oder mehr Oberflächen.
Technische Oberflächen bilden in der Regel Kompartimente aus zylindrischen, konischen, helixförmigen Flächen, Ebenen, Kugeln und Tori, die durch bestimmte Bilder und Dimensionen gekennzeichnet sind.
Die Elemente des Teils werden in Standardelemente mit Standardformen, -bildern und -größen (Keilnuten, Fasen, Nuten usw.) und Nichtstandardelemente (Abflachungen, Vorsprünge usw.) unterteilt.
Die geometrische Form eines Teils wird durch die Form und relative Position der es bildenden Strukturelemente bestimmt, deren Oberflächen die Gegen-, angrenzenden (Mattierungs-) und freien Oberflächen des Teils bilden.
Passende und angrenzende Flächen Kontaktdetails -
mit den Oberflächen anderer Teile verbinden und mit ihnen formen bewegliche Gelenke(Translation, Rotation, Schraube usw.) und feste Verbindungen, Sicherstellung der relativen Position und Ausrichtung der Teile sowie der Übertragung auftretender Kräfte. In diesem Fall sind die Kontaktflächen weiblich oder männlich, die angrenzenden Flächen jedoch nicht. An die Bearbeitungsgenauigkeit und Rauheit dieser Oberflächen werden erhöhte Anforderungen gestellt.
Freie Flächen Teile dürfen nicht mit den Oberflächen anderer Teile in Berührung kommen. Sie fassen alle Flächen zu einer zusammen und sorgen für deren gewünschte Lage, Ausrichtung und Kraftübertragung innerhalb des Bauteils.
Wird in Zeichnungen verwendet drei Arten von Bildern, Darstellung der Form, Position und Ausrichtung eines Teilelements: präzise
Die Intensivierung der Produktion im Maschinenbau ist untrennbar mit der technischen Umrüstung und Modernisierung der Produktionsmittel unter Nutzung der neuesten Errungenschaften von Wissenschaft und Technik verbunden. Die technische Umrüstung und Produktionsvorbereitung umfasst zwangsläufig die Prozesse des Entwurfs technologischer Geräte und ihrer Herstellung.
Etwa 50 % des Gesamtvolumens der technologischen Ausrüstung sind Werkzeugmaschinen. Der Einsatz von Werkzeugmaschinen ermöglicht:
Das Werkstück sicher abstützen und sichern und gleichzeitig seine Bearbeitung bewahren;
Stellen Sie stets eine hohe Qualität der verarbeiteten Teile sicher
mit minimaler Abhängigkeit der Qualität von der Qualifikation der Arbeitnehmer;
Steigerung der Produktivität und Erleichterung der Arbeitsbedingungen der Arbeiter bei der Mechanisierung von Geräten;
Erweitern Sie die technologischen Fähigkeiten der verwendeten Geräte.
Je nach Art der Produktion sind das technische Niveau und der Aufbau von Werkzeugmaschinen unterschiedlich. In der Massen- und Großserienfertigung werden in den meisten Fällen spezielle Einzweck-Werkzeugmaschinen eingesetzt, um bestimmte Bearbeitungsvorgänge an einem bestimmten Teil durchzuführen. Diese Geräte sind am arbeitsintensivsten und teuersten in der Herstellung. Unter Bedingungen der Einzel- und Kleinserienfertigung hat sich ein System universeller vorgefertigter Geräte durchgesetzt, das auf der Verwendung von Standardteilen und Baugruppen basiert. Dieser Gerätetyp ist hinsichtlich der Produktionsvorbereitung mobiler und erfordert keine nennenswerten Kosten.
Teilbuchsenmaschine
Die Herstellung jeglicher Art von Werkzeugmaschinen, die den Produktionsanforderungen entsprechen, erfordert zwangsläufig den Einsatz qualifizierter Arbeitskräfte.
IN In letzter Zeit Auf dem Gebiet der Werkzeugmaschinenkonstruktion wurden erhebliche Fortschritte erzielt. Es wurden Methoden zur Berechnung der Genauigkeit von Bearbeitungsteilen in Werkzeugmaschinen entwickelt, Präzisionsspannfutter und -dorne geschaffen, Spannmechanismen verbessert und die Methodik für deren Berechnungen verbessert sowie verschiedene Antriebe mit Elementen entwickelt, die ihre erhöht haben Betriebssicherheit.
Die vorgelegte Erläuterung enthält die Informationen, die erforderlich sind, um eine Werkzeugmaschinenvorrichtung zur Herstellung eines Durchgangsgewindelochs in der „Glühbirne“ so einfach, zuverlässig und leicht zu handhaben wie möglich zu berechnen, zu entwerfen und herzustellen und dabei den Standards und Anforderungen der Produktion gerecht zu werden ”Teil unter mittleren Produktionsbedingungen.
1. Allgemeiner Teil
1.1 Beschreibung des Teils, Analyse der Herstellbarkeit des Teils
Der Teil „Buchse“ gehört zur Gruppe der rotierenden Körper mit den Gesamtabmessungen 120mm×130mm. Das Teil besteht aus einer zylindrischen Basis und zwei symmetrisch angeordneten zylindrischen Vorsprüngen. Der zylindrische Sockel ist ein schwarzer Sockel und hat einen Durchmesser von 120 mm und eine Höhe von 40 mm. Auf der zylindrischen Oberfläche der Nabe mit einem Durchmesser von 96h14 befindet sich eine durchgehende Gewindebohrung mit einem Durchmesser von 8 mm und einer Tiefe von 20 mm. Auf der zylindrischen Oberfläche einer Nabe mit einem Durchmesser von 96h9 befindet sich eine 2,5 mm breite technologische Nut. Der „Glühbirnen“-Teil hat ein zentrales, glattes, abgestuftes Durchgangsloch mit einem Durchmesser von 56 mm bis zu einer Tiefe von 40 mm, einem Durchmesser von 35 x 11 mm und einem Durchmesser von 56 mm bis zu einer Tiefe von 40 mm.
Teile vom Typ „Bush“ werden in Bohrgeräten verwendet (zur Zentrierung und zur Beseitigung der Möglichkeit eines Bohrerrückzugs); zum Einbau in Kugellagergelenke, zur Sicherung, Begrenzung des Verschleißes und des Vorstehens von Gegenstücken.
Abb. 1 3D-Modell des Teils
Als Ergebnis der Analyse der Zeichnung des Teils „Buchse“ ist klar, dass
Die Zeichnung enthält alle notwendigen Angaben zu Maßen, Genauigkeit, Qualität der bearbeiteten Oberflächen und zulässigen Abweichungen von der korrekten geometrischen Form. Es werden Anweisungen zum Material Stahl 25 GOST 1050-88 gegeben
Das Design des Teils ist technologisch:
Es ist erlaubt, die Oberflächen des Teils pro Durchgang zu bearbeiten;
Zur Bearbeitung werden handelsübliche Schneid- und Messwerkzeuge verwendet.
Die Vervollständigung aller Oberflächen gewährleistet eine bequeme Bereitstellung von Standard-Schneidwerkzeugen
Das Teil hat gute Grundflächen.
Es ist möglich, dem Prinzip zu folgen und die Grundflächen zu kombinieren.
Bei der Auswahl der technischen Grundflächen für die Installation wird das Prinzip der Kombination von Design und technologischen Grundlagen beachtet.
Es gibt keine Elemente, die die Arbeitsintensität des Teils erhöhen. Das Design des Teils weist ein zentrales, glattes Stufenloch auf, was die visuelle Beobachtung des Schneidvorgangs und der Spanabfuhr erschwert.
1.2 Materialeigenschaften
Teilmaterial Stahl 25 GOST 1050-88 – Strukturkohlenstoffqualitätsstahl
Tabelle 1 Chemische Zusammensetzung
Tabelle 2 Mechanische Eigenschaften
Tabelle 3 Physikalische Eigenschaften
T | E 10-5 | A106 | ICH | R | C | R 109 |
Hagel | MPa | 1/Grad | W/ (m Grad) | kg/m3 | J/ (kg Grad) | Ohm m |
20 | 1.98 | 7820 | 169 | |||
100 | 1.96 | 12.2 | 51 | 470 | 219 | |
200 | 1.91 | 13.0 | 49 | 483 | 292 | |
300 | 1.86 | 13.7 | 46 | 381 | ||
400 | 1.63 | 14.3 | 43 | 521 | 488 | |
500 | 14.7 | 40 | 571 | 601 | ||
600 | 15.0 | 36 | 758 | |||
700 | 15.2 | 32 | 925 | |||
800 | 26 |
Physikalische Eigenschaften von Stahl 25 (ST 25, ST25):
T – Temperatur, bei der diese Eigenschaften erreicht wurden, [Grad]
E – Elastizitätsmodul erster Art, [MPa]
a - Wärmeausdehnungskoeffizient (linear) (Bereich 20o - T),
l – Wärmeleitfähigkeitskoeffizient (Wärmekapazität von Stahl), [W/ (m Grad)]
r - Stahldichte, [kg/m3]
C – Spezifische Wärmekapazität von Stahl (Bereich 20o – T), [J/ (kg Grad)]
R – Elektrischer Widerstand, [Ohm·m]
Technologische Eigenschaften
Achsen, Wellen, Kupplungen, Sperrklinken, Hebel, Gabeln, Unterlegscheiben, Wellen, Bolzen, Flansche, T-Stücke, Befestigungselemente und andere nicht wesentliche Teile;
Nach der chemischen Behandlung – Schrauben, Buchsen, Sperrklinken und andere Teile, an die hohe Oberflächenhärte und Verschleißfestigkeit bei geringer Kernfestigkeit gestellt werden.
Ersetzt Stahl 30, Stahl 25N
1.3 Verarbeitungsweg
Tabelle 4
Ausrüstung |
Werkzeug |
Werkzeug |
||
005 | Beschaffung. Stempeln Sie das Werkstück gemäß den technischen Spezifikationen. OGMet-Prozess. |
Warmschmiedepresse | - | |
010 | Prüfen. Kontrollieren Sie die Materialqualität und die Abmessungen des Werkstücks anhand der Zeichnung. |
OTK-Tabelle | - | Messschieber ШЦ-I-150-0.1GOST 166-80 |
015 | Drehen. |
Schraubendrehmaschine SM-300E |
(Platte GOST 2882-74) |
Messschieber ШЦ-I-150-0.1 GOST 166-80 |
020 | Drehen A. Installieren und sichern Sie das Werkstück 03. Schärfen Ø100h12 0,6 Fasenbildung 1,5x45 0,8 Bohrung 35Н11 0,9 Fasenbildung 1,5x45 |
Schraubendrehmaschine SM-300E | Der Schneider ist schlecht. gebogen T14K8 GOST 18891-73 Schubschneider GOST 18879-73 Dauerbohrschneider GOST 18883-73 Bohrschneider GOST 18882-73 |
Messschieber ШЦ-I-150-0.1 GOST 166-80 Vorlagen. GOST 18123-82 Halterung Ø 96h9 GOST 18360-93; Rauheitsproben GOST 9378-93 |
025 | Bohren. A. Installieren und sichern Sie das Werkstück T. Spezial Anpassung 01. Bohren Sie ein Loch Ø8 03. Fäden abschneiden |
Rapidrill 450 | Wendelbohrer Ø8 T5K10 GOST 20695-75 Senker GOST 14953-80 Kurzer Hahn GOST 3266-81 |
Messschieber ШЦ-I-150-0.1GOST 166-80 Rauheitsproben GOST 9378-93 |
030 | Schlosserwerkstatt. Grate und stumpfe scharfe Kanten entfernen. |
Basteltisch. | Schlosserwerkzeug | - |
035 | Prüfen. Kontrollieren Sie die Abmessungen des Teils gemäß der Zeichnung. |
OTK-Tabelle | Messschieber ШЦ-I-150-0.1 GOST 166-80 Rauheitsproben GOST 9378-93 Vorlagen. GOST 18123-82 Halterung Ø 96h9 GOST 18360-93; Kaliberstopfen Ø 35H11 GOST 14807-69; |
Installationstechnische Grundlagen
Abb.2 (U.T.B.)
Tabelle 5
Name und Inhalt des Vorgangs | Ausrüstung | U.T.B. | Gerät | |
015 | Drehen. A. Installieren und sichern Sie das Werkstück T.3-Kul. Patrone GOST-2675-80 01. Schneiden Sie das Ende auf die Größe 134h14 zu; 02. Ø100h14 auf eine Länge von 45 mm schärfen, um eine Schulter zu bilden. 03. Schleifen Sie eine Fase 1,5x45˚ auf Ø96 mm 04. Bohren Sie ein Loch Ø 52H14 auf eine Länge von 40 mm |
Schraubendrehmaschine SM-300E | 3; 4 | 3-Backenfutter GOST 2675-80 |
020 | Drehen A. Installieren und sichern Sie das Werkstück T.3-Kul. Patrone GOST-2675-80; geteilter Ärmel. 01. Schneiden Sie das Ende auf Größe 132 zu; 02. Ø 106h14 auf eine Länge von 45 mm schärfen, um eine Schulter zu bilden 03. Schärfen Ø100h12 0,4 Eine 1,5 mm breite Nut schleifen 0,5 Ø 96h9 auf eine Länge von 45 mm schärfen 0,6 Fasenbildung 1,5x45 0,6 Bohren Sie das Loch Ø52Н14 auf eine Länge von 40 mm, um eine Schulter zu bilden 0,7 Bohrloch Ø31Н14 0,8 Bohrung 35Н11 0,9 Fasenbildung 1,5x45 |
Schraubendrehmaschine SM-300E | 1; 2 | 3-Backenfutter GOST 2675-80 mit geteilter Buchse |
025 | Bohren. A. Installieren und sichern Sie das Werkstück T. Spezial Anpassung 01. Bohren Sie ein Loch Ø8 02. Senken Sie das Loch auf eine Tiefe von 1,6 mm 03. Gewinde M8-7N schneiden |
Rapidrill 450 | 5 | Spezielles Gerät |
1.4 Auswählen eines Teileplatzierungsschemas
Bei der Gestaltung eines technologischen Bearbeitungsprozesses werden für jeden Arbeitsgang die Montagebasen des Werkstücks ausgewählt, von denen die Genauigkeit der Werkstückbearbeitung abhängt. Die Anlage des Werkstücks an den Grundflächen in der Vorrichtung bestimmt seine Position relativ zum Schneidwerkzeug. Daher wird man sich bei der Auswahl der Grundflächen an der Regel des „Kombinierens von Grundflächen“ orientieren, nämlich danach streben, technologische Installationsgrundlagen mit Design- und Messgrundlagen zu kombinieren. Die Art der Montage eines Teils zur Bearbeitung auf einer Maschine wird unter Berücksichtigung der Art der Produktion ausgewählt. Bei der Serienfertigung im mittleren Maßstab wird das auf der Maschine zu bearbeitende Teil direkt in die Vorrichtung eingebaut. Gemäß der Bearbeitungsroute für Vorgang 035 Bohren ist es notwendig, ein Durchgangsloch für das M8-7H-Gewinde zu bohren, es anzufasen und das M8-7H-Gewinde zu schneiden. Der Vorgang wird auf einer Vertikalbohrmaschine Modell 2M112 mit einem Spiralbohrer Ø6,7 T5K10 GOST 20695-75 durchgeführt (Abb. 4).
Senker GOST 14953-80 (Abb. 3)
Fertigstellung:
D | d 1 | d 3 | L | l 1 | l 2 |
8 | 8.0 | 7.0 | 72 | 2.5 | 13 |
Um das Teil während des Bohrvorgangs zu stützen, werden die folgenden Basisflächen ausgewählt:
Enddurchmesser 96h14 und zwei Außendurchmesser 96h14 und 96h9.
Durch diese Lagerung wird sichergestellt, dass das Werkstück über fünf Freiheitsgrade verfügt.
Das verwendete Gerät ist etwas Besonderes.
Kellerschema.
(Abb.6) Teilepositionsdiagramm
1.5 Auswahl der Ausrüstung für den Betrieb (Eigenschaften und Modell der Maschine)
Bohrmaschine Modell Rapidrill 450
Maschinenfunktionen
Leistungsstarkes Schnellbohr- und Gewindeschneidzentrum mit Eilgang von 48 m/min
Hohe Präzision und Vorschübe durch Linearführungen kombiniert mit Kugelumlaufspindeln
Schneller Werkzeugwechsler mit 12 Werkzeugen, Werkzeug-/Werkzeugwechselzeit 1,4 Sek. (Rapidrill 450)
Hauptspindel mit Drehzahl bis 8000 min-1 (Standard) oder bis 12000 min-1 (optional)
Leistungsstarker AC-Servoantrieb für die Hauptspindel mit einer Leistung von 5,5 kW
Die serienmäßige Ausstattung mit einem Späneförderer sorgt für eine störungsfreie Späneabfuhr
Geringe Vibrationen der Maschine aufgrund der schweren Konstruktion
Datenein- und -ausgabe über RS-232-Schnittstelle oder Speicherkarte, Designgruppen optimal angeordnet
Riemenantrieb für das Modell Rapidrill 450
Tabelle.6
Technische Spezifikationen | Einheit ändern | Radidrill 450 |
Desktop | ||
Tischgröße | mm | 500x320 | Kg | 200 |
T-Pyzes (Anzahl x Breite x Abstand) | Mm | 3x14x100 |
Hauptspindel | ||
Leistung des Hauptspindelmotors | kW | 3.7 |
Rotationsfrequenz | min-1 | 8000 |
Werkzeuge | ||
Anzahl der Positionen | setzt | 12 |
Werkzeugwechselzeit | ||
Werkzeug/Instrument | Sek | 1.4 |
Klemme | Sek | 2.4 |
Werkzeuggewicht (maximal) | kg | 2,5 |
Werkzeuglänge (maximal) | mm | 200 |
Werkzeugdurchmesser (maximal) | mm | 80 |
Genauigkeit | ||
Positioniergenauigkeit | mm | 0,01 |
Wiederholgenauigkeit | mm | 0,008 |
Abmessungen (LxBxH) | mm | 1200 x 2280 x 2330 |
Gewicht | kg | 2100 |
1.6. Berechnung der Schnittkräfte für eine Operation
Die Schnittkräfte werden nur für das Bohren berechnet, da bei der Bearbeitung ein kombiniertes Bohrer-Senker-Werkzeug verwendet wird und die größte Axialkraft beim Bohren eines Lochs auftritt.
Allgemeine Maschinenbaunormen für Zeit- und Schnittarten zur Regelung von Arbeiten an Universal- und Mehrzweckmaschinen mit numerischer Steuerung.
Tabellenwerte der Schnittmodi beim Bohren.
S von =0,19 mm/U
Vt =25,5 m/min
Rt =1885 N
Nt =0,64 kW
S von - Tischvorschub mm/U;
Р t – tabellarische axiale Schnittkraft, N [Seite 126, Karte 46, Blatt 1];
V t – Tischgeschwindigkeit m/min;
N t - tabellarische Leistung, kW [Seite 126, Karte 46, Blatt 1];
Innings S, mm/U:
S= S von · KSM, mm/U
S von - Tischvorschub mm/U
K SM - 1,3 Korrekturfaktor für den Vorschub, abhängig vom Werkstückmaterial [Seite 143, Karte 53, Blatt 1];
S = 0,19 · 1,3 = 0,247 mm/U;
Bohrgeschwindigkeit V, m/min:
V= V t K v m K v z · K v f · K v t K v p · K v und KvL Kvw, m/min
V t - Tischgeschwindigkeit m/min
K vm - 1,3 Geschwindigkeitskorrekturfaktor, abhängig vom Werkstückmaterial [Seite 143, Karte 53, Blatt 1];
K vl - 0,8 Drehzahlkorrekturfaktoren für veränderte Betriebsbedingungen je nach Kühlanwendung [Seite 145, Karte 53, Blatt 3];
K vw - 0,8 - Gfür geänderte Betriebsbedingungen in Abhängigkeit vom Zustand der Werkstückoberfläche [Seite 145, Karte 53, Blatt 3];
K vз - 1,0 Korrekturfaktoren für die Umformgeschwindigkeit und das Schärfen des Werkzeugs [Seite 146, Karte 53, Blatt 4];
K vт - 1,0 Korrekturfaktoren für die Geschwindigkeit bei veränderten Betriebsbedingungen, abhängig vom Verhältnis der tatsächlichen Widerstandsdauer zur Standarddauer [S. 148, Karte 53, Blatt 6];
K vп – 1,0 Gfür geänderte Betriebsbedingungen in Abhängigkeit von der Beschichtung des Werkzeugmaterials [Seite 147, Karte 53, Blatt 5];
K vн – 1,43 Korrekturfaktoren für die Geschwindigkeit des Instrumentenmaterials [Seite 146, Karte 53, Blatt 4];
K vL - 1,0 Korrekturfaktoren für die Geschwindigkeit der Länge des Arbeitsteils des Bohrers [Seite 146, Karte 53, Blatt 4];
V = 25,5 1,3 0,8 0,8 1,0 1,0 1,43 1,0 1,0 = 30,33 m/min
Einfädelgeschwindigkeit V, m/min:
V= V t K v m K vk , m/min
V t – Tischgeschwindigkeit, m/min; K V m - 1,3 Geschwindigkeitskorrekturfaktor [Seite 143, Karte 53, Blatt 1]; K vk - 1,0 Gfür veränderte Betriebsbedingungen in Abhängigkeit vom Grad der Gewindegenauigkeit [Seite 149, Karte 53, Blatt 7];
V = 25,5 1,3 1,0 = 33,15 m/min
Schneidkraft beim Bohren N, kW:
N= Nt/ K N·m, kW
N t – tabellarische Leistung, kW [Seite 126, Karte 46, Blatt 1], K N m – 1,3 Korrekturfaktor für Leistung [Seite 143, Karte 53, Blatt 1];
N = 0,64/1,3 = 0,49 kW
Axialkraft beim Bohren P, N:
P = P t /K Pm, N
Р t – tabellarische axiale Schnittkraft, N [Seite 126, Karte 46, Blatt 1]
K Рм – Korrekturfaktor für Axialkraft [Seite 143, Karte 53, Blatt 1]; K Рм = 1,3
P = 1885/1,3 = 1450 N
2. Berechnungsteil
2.1 Bestimmung des Basisfehlers
Der Basisfehler ist die Differenz der maximalen Abstände der Messbasis relativ zum installierten Schneidwerkzeug bei einer bestimmten Werkstückgröße. Ein Positionierungsfehler tritt auf (Abb. 8), wenn die Referenzmontagebasis des Werkstücks nicht mit der Messbasis ausgerichtet ist.
(Abb.8) Standortdiagramm
Aufgrund der Tatsache, dass die Installations- und Messbasen entlang des 130-mm-Endes ausgerichtet sind, ist der Fehler für die Größe 23 ± 0,1 gleich 0.
2.2 Berechnung der erforderlichen Spannkraft des Werkstücks
Da die Schnittkraft und die Spannkraft in die gleiche Richtung gerichtet sind, fallen sie zusammen. IN in diesem Fall Schnittkraft – das ist die Axialkraft beim Bohren = 1450 (N), siehe Seite 19
Berechnung der Spannkraft.
η - Effizienz unter Berücksichtigung der Reibungsverluste zwischen der Klemmleiste 3 und ihrer Halterung ( η = 0,95)
Für die Anfangskraft P o nehmen wir:
Multiplizieren Sie die Anfangskraft P o mit der Länge des Griffs (L) und dem Durchmesser der Schraube (d).
R o - Anfangskraft 140…200 N ;
L- Grifflänge 14, mm
D- Schraubendurchmesser 5mm
1)
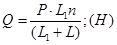
2)
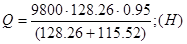
3)
Berechnung des Nennaußendurchmessers der Schraube.
[σ ð ] - zulässige Zugspannung ([σ ð ] = 58…98 MPa.)
Schrauben und Muttern bestehen aus Stahl 35; 45 GOST 1050-88;
Härte HRC30…35
3) ; mm
3. Designteil
3.1 Auswahl der Leuchteneinbauelemente
Die Montageelemente (Stützen) der Vorrichtungen dienen dazu, die Grundflächen des Werkstücks darauf zu montieren.
Die Anzahl und Lage der Montageelemente muss die notwendige Ausrichtung des Werkstücks entsprechend dem im technologischen Prozess übernommenen Grundschema gewährleisten.
Kellerschema.
Das Werkstück wird in einer Vorrichtung mit zwei Außendurchmessern und einer Betonung am Ende befestigt. Folglich sind die Installationselemente in diesem Gerät Prismen.
Prismen dienen zur Montage von Teilen auf der äußeren Zylinderfläche und sind für die Unterlage von Teilen mit Æ 5 - 150 mm vorgesehen. Material - Stahl 20Х GOST 4543-71; Härte der Arbeitsflächen HRC 55 - 60; Zementierung bis zu einer Tiefe von 0,8 - 1,2 mm.
(Abb.12) (Abb.13)
Zur präzisen Montage von Prismen am Gerätekörper werden Steuerstifte verwendet , Prismen werden mit Schrauben am Körper befestigt .
3.2 Auswahl der Spannmittel
Die Gründe für die Wahl des Klemmmechanismustyps sind:
Das Gerät ist für die Bearbeitung von Werkstücken in der Serien- und Mittelserienfertigung konzipiert.
Die Schnittkraft für diesen Bohrvorgang beträgt =1450N (siehe Seite 21)
Um den Kontakt des Werkstücks mit den Montageelementen des Gerätes beim Befestigen sicherzustellen, wähle ich den Angriffspunkt der Spannkraft so, dass die Wirkungsrichtung senkrecht zur Oberfläche des Tragelements verläuft.
Bei der Auswahl einer Spannvorrichtung orientiere ich mich an folgenden Anforderungen:
Verändern Sie beim Spannen nicht die ursprünglich vorgegebene Position des Werkstücks.
Die Spannkraft muss eine zuverlässige Befestigung des Teils gewährleisten und ein Verschieben, Drehen und Vibrieren des Werkstücks während der Bearbeitung auf der Maschine verhindern.
Das Spannen und Lösen des Werkstücks erfolgt mit minimalem Kraft- und Arbeitsaufwand. Bei Verwendung von manuellen Klemmen sollte die Kraft N nicht überschreiten. (siehe Seite 21)
Der Spannmechanismus muss einfach aufgebaut, kompakt sowie möglichst komfortabel und sicher in der Handhabung sein (minimale Gesamtabmessungen und Anzahl abnehmbarer Teile; die Spannmechanismus-Steuervorrichtung muss sich auf der Seite des Arbeiters befinden).
Basierend auf dem oben Gesagten wird in dieser Werkzeugmaschine ein Prisma verwendet.
1 - Gerätekörper
2 - Frühling
4 - Verstellbare Stütze
5 - Prismatische Backe
3.3 Auswahl und Begründung des Kraftantriebs
Nachdem ich das Design der Spannvorrichtungen ausgewählt habe, wähle ich das Design des Kraftantriebs, um diese beim Spannen und Lösen des Werkstücks in der Vorrichtung zu bewegen.
Ich wähle das Antriebsdesign basierend auf den spezifischen Einsatzbedingungen aus:
Art der Produktion - seriell, mittlerer Maßstab;
der Wert der Schnittkraft P = 1450 [N] (siehe Seite 21), die während der Bearbeitung auf das Werkstück einwirkt,
Konstruktionsmerkmale des Werkstücks, nämlich das Material des zu bearbeitenden Werkstücks ist eine Aluminiumlegierung, die sich leicht verformen lässt.
Maschinentyp - Radialbohrmaschine 2M112
Die Spannvorrichtung in der Vorrichtung wird direkt angetrieben, indem der Arbeiter die Anfangskraft P auf den Arm L ausübt (mit einem Schraubenschlüssel).
Diese Geräte werden manchmal auch handbetätigte Spanngeräte genannt.
4. Designteil
4.1 Montage der Vorrichtung an der Maschine
Um das Gerät auf der Arbeitsfläche des Tisches zu befestigen, befinden sich an der Unterseite des Gehäuses Laschen, in die Befestigungsbolzen eingesetzt werden. Die Schraubenköpfe werden in T-Nuten am Tisch gehalten.
Die Anzahl der Bolzen und damit der Laschen wird in Abhängigkeit von den aktuellen Schnittkräften gewählt. In den meisten Fällen ist es möglich, mit zwei Laschen auszukommen und nur bei hohen Schnittkräften ist es notwendig, vier vorzusehen – zwei auf jeder Seite. Bei vier Laschen stimmt der Abstand t zwischen ihnen mit dem Abstand der T-förmigen Schlitze des Maschinentisches überein.
Oftmals ist es erforderlich, der Vorrichtung eine ganz bestimmte Position auf dem Maschinentisch in Bezug auf die Längsvorschubrichtung des Tisches zu geben. In diesem Fall erfolgt die Ausrichtung des Geräts über Schlüssel entlang der T-förmigen Schlitze des Tisches, deren Richtung genau mit der Richtung seines Längsvorschubs übereinstimmt. Am weitesten verbreitet sind standardmäßige prismatische Schraubenschlüssel (GOST l4737-69) (Abb. a). Die Hauptgröße des Schlüssels ist die Breite B, die der Breite der T-förmigen Nut des Tisches entsprechen sollte. Maß B wird nach h8 nach ST SEV (C3 nach GOST) ausgeführt. Bei Schlüsseln mit Nut wird davon ausgegangen, dass die Größe B 1 (an der Basis) 0,5–1,0 mm größer ist als die Breite B, die erforderlich ist, um den Schlüssel entlang der T-förmigen Nut des Tisches zu passen.
Montage von Vorrichtungen mit Schlüsseln an Fräsmaschinen
An jedem Gerät sind zwei Schlüssel angebracht. Der Schlüssel 2 wird von unten in eine speziell dafür vorgesehene Nut B am Gehäuse 1 des Gerätes montiert und mit der Schraube 3 befestigt (Abb. b).
Die Schlüssel sind so positioniert, dass sie beide in die gleiche T-förmige Nut des Tisches passen – normalerweise in die mittlere, da diese genauer ist (Abb. c)
Ösen für Befestigungsschrauben sind angebracht: mit zwei Ösen – auf der Achse der Schlüssel, mit vier – links und rechts von der Achse, sodass die seitlichen Nuten des Tisches zur Befestigung genutzt werden können.
Aufgrund von Verschleiß und späteren Reparaturen liegt die Breite der Schlitze an Maschinentischen oft außerhalb der Toleranz, was zu größeren Lücken zwischen dem Spannschlüssel und der Tischnut führt. Um eine mögliche Drehung des Geräts auf dem Tisch während der Montage zu verhindern, wird es in diesen Fällen mit Schlüsseln auf eine Seite der Tischnut gedrückt und dadurch der Positionierungsfehler an der Maschine verringert.
Abschluss
Der Einsatz von Werkzeugmaschinen ermöglicht:
· Reduzieren Sie Haupt- und Nebenzeiten, indem Sie das Markieren von Werkstücken vor der Bearbeitung eliminieren.
· Erhöhung der Verarbeitungsgenauigkeit.
· Erleichterung der Arbeit des Maschinenbedieners, Einsatz von Arbeitskräften mit geringerer Qualifikation.
· Steigerung der Arbeitsproduktivität.
· die technologischen Fähigkeiten von Maschinen erweitern.
· Bedingungen für die Automatisierung und Mechanisierung von Werkzeugmaschinen schaffen.
· die Herstellungskosten der Produkte senken.
Referenzliste
1. Goroshkin A.K. Zubehör für Metallschneidemaschinen. - M. - Maschinenbau 1990
2. Kasilova A.G. und Meshcheryakov R.K. Handbuch des Technologen - Maschinenbauingenieurs. In 2 Bänden. - M. - Maschinenbau 1985
3. Schatilow A.A. Nachschlagewerk für Werkzeugmaschinen. T1 M. - Maschinenbau 1984
MOSKAUER AUTOMOBIL- UND STRASSENINSTITUT (STAATLICHE TECHNISCHE UNIVERSITÄT)
O.A.OGANESOV, N.N.KUZENEVA
INFORMATION
MATERIAL
LERNPROGRAMM
MOSKAU 2008
UDC 744:621:72 BBK 30,11:34,4:38,712
Oganesov O.A., Kuzeneva N.N. Technische Grafiken. Referenzmaterialien: Lehrbuch/MADI(GTU). Teil 3. -M., 2008. -93p.
Gutachter: Ph.D. Technik. Wissenschaften, Professor O.V. Georgievsky (MGSU), Ph.D. Technik. Naturwissenschaften, außerordentlicher Professor P.R. Dobrogaev MADI (GTU).
Der letzte dritte Teil des Handbuchs beschreibt die allgemeinen Regeln für die Erstellung von Teilezeichnungen, einschließlich ihrer Skizzen, und Zeichnungen von Baugruppen und gibt außerdem Empfehlungen für die Detaillierung einer allgemeinen Zeichnung, einschließlich deren Lektüre. Das Handbuch enthält Arbeitszeichnungen von Teilen, die häufig in Maschinenkonstruktionen verwendet werden, mit Standardbildern und Originalteilen.
Das Lehrbuch richtet sich an MADI-Studenten (GTU) im ersten bis zweiten Studienjahr, die technische Grafik studieren, und kann für ältere Maschinenbaustudenten beim Abschluss von Kursarbeiten und Projekten hilfreich sein.
© Moskauer Institut für Automobil- und Straßenwesen (Staatliche Technische Universität), 2008
12. DETAILZEICHNUNGEN
12.1. Arten von Produkten und Designdokumenten
Ein Produkt ist ein beliebiger Artikel oder eine Gruppe von Artikeln, die hergestellt werden sollen. In der Ingenieurgrafik-Schulung werden von Produkten nur Teile und Baugruppen berücksichtigt.
Ein Teil ist ein nicht spezifiziertes Produkt, das aus einem homogenen Material besteht und keine Komponenten aufweist, die durch Montagevorgänge verbunden werden müssen.
Montageeinheit- ein bestimmtes Produkt, dessen Bestandteile durch Montagevorgänge – Schrauben, Schweißen, Löten, Nieten, Bördeln usw. – miteinander verbunden werden.
Die Zusammensetzung und das Design des Produkts werden durch die in GOST 2.102-68* festgelegten Designdokumente bestimmt. Wird in Bildungseinrichtungen verwendet Trainingszeichnungen - Teilezeichnungen, Montagezeichnungen, Übersichtszeichnungen und Spezifikationen, die sich geringfügig von den Prunterscheiden.
12.2. Teilezeichnung und Grundvoraussetzungen dafür
Eine (Arbeits-)Zeichnung eines Teils ist das Hauptkonstruktionsdokument, das Bilder des Teils und andere für seine Herstellung und Kontrolle erforderliche Daten enthält. Die Qualität des Teils hängt von seiner korrekten Ausführung ab.
Das Teil in der Zeichnung ist in seiner fertigen Form mit den Formen und Abmessungen dargestellt, die es vor dem Zusammenbau haben sollte.
Teilezeichnungen werden je nach Zweck und Ausführungsart in Skizzen (siehe 12.7) und tatsächliche Teilezeichnungen unterteilt, auf die weiter eingegangen wird.
Die Tutorial-Zeichnung des Teils enthält Bilder und Abmessungen des Teils., die seine Form vollständig widerspiegelt, sowie
Informationen zu Name und Material des Teils, Maßstab, Anzahl der Zeichnungsblätter, sein Testamentsvollstrecker und der Lehrer, der die Zeichnung entgegennimmt, im Titelblock angegeben. Die Zeichnung kann Beschriftungen enthalten, die die Bilder des Teils mit Informationen zu dessen Parametern, Material, individuellen Abmessungen usw. ergänzen.
Eine Übungszeichnung eines Details wird auf einem Blatt Whatman-Papier mit einem Zeichenwerkzeug im Standardmaßstab erstellt und gemäß den Standards für Formate, Linien, Schriftarten usw. erstellt.
Das Hauptkriterium für die Bewertung einer Zeichnung ist ihre Benutzerfreundlichkeit., abhängig von der Anzahl der Bilder des Produkts, ihre gegenseitige
Standort, Größe, Maßstab usw.
ZU Die Anzahl der Bilder und Abmessungen in der Zeichnung sollte minimal sein, aber ausreichend, um die äußeren und inneren Formen des Teils vollständig sichtbar zu machen und die Reversibilität der Zeichnung sicherzustellen. Es ist zulässig, mehr als die Mindestanzahl an Bildern bereitzustellen, wenn dies die Lesbarkeit der Zeichnung erheblich erleichtert. Allgemeine Regeln für die Erstellung von Bildern von Teilen und Zeichnungsmaßen auf der Zeichnung werden von GOST festgelegt 2.305-68* und GOST 2.307-68*.
Bei der Auswahl einer Skala Zeichnungen berücksichtigen die Komplexität der Form des Teils, seine tatsächlichen Abmessungen und das Verhältnis zwischen den Größen der einzelnen Elemente des Teils.
Im Schulungskurs werden alle Zeichnungen auf einem Blatt erstellt, daher ist in der Spalte „Blätter“ der Hauptbeschriftung „1“ angegeben.
Zeichenpapiergröße Die Auswahl erfolgt unter Berücksichtigung der Anzahl der Bilder, ihres Layouts, ihres Maßstabs und ihrer einfachen Größenanpassung. Es wird empfohlen, dass Bilder nach Möglichkeit 40–50 % und Bilder und Abmessungen 70–80 % der Blattfläche einnehmen.
Übungszeichnungen von Teilen werden anhand des fertigen Teils erstellt.,nach einer Skizze eines Teils oder einer Gesamtansichtszeichnung einer Baugruppe, bei dem das Teil ein integraler Bestandteil des Produkts ist.
12.3. Teilegruppen Es gibt drei Gruppen von Teilen:
1. Standardteile, gekennzeichnet durch praktische Formen und eine große Auswahl an Größen (Bolzen, Muttern, Dübel usw.). Arbeitszeichnungen dieser Teile sind in den einschlägigen Normen enthalten, die die Form des Teils, seine Abbildungen in der Zeichnung, Abmessungen und Regeln für ihre Anwendung regeln.
2. Teile mit Standardbildern:
- Teile, deren Bilder vollständig durch Normen geregelt sind (Federn), und Teile, die die Form von Normteilen haben, sich jedoch in mehreren Größen von diesen unterscheiden. Bilder und Regeln für die Dimensionierung dieser Teile sind durch Standards festgelegt, die Größenwerte jedoch nicht;
- Teile, deren Hauptelemente Standardbilder, Größen und Regeln für ihre Anwendung haben (Teile mit Getriebeelementen, Rohrleitungen usw.);
- Teile aus Sorten- und Plattenmaterial mit teilweise regulierten Bildern und Abmessungen.
3. Originalteile, deren Form ganz oder teilweise von der Form von Standardteilen abweicht und mit Standardbildern.
Dementsprechend werden Teilezeichnungen in Zeichnungen von Normteilen mit Standardbildern und Originalzeichnungen unterteilt.
12.4. Arten von Teilen und ihre Elemente
Teile werden nach Design und technologischen Merkmalen unterschieden.
Designteiltyphängt von seinem Zweck und seinen betrieblichen Funktionen ab.Technologische Art des Teils(gegossen, gestanzt usw.) bestimmt die Art seiner Hauptbearbeitung, die der Form des Teils besondere charakteristische Merkmale verleiht.
Jeder Teil ist eine bestimmte Menge von Elementen, die zu einem Ganzen zusammengefasst sind.
Ein Element eines Teils ist ein separater Teil davon, der seinen eigenen Zweck hat (Löcher, Nuten, Abflachungen, Gewinde usw. – siehe Abb. 12.1).
Je nach Zweck werden die Elemente eines Teils in strukturelle, technologische und informative Elemente unterteilt.
(Slot)
Nut (Nut)
Rille
Nutloch Blinddurchgangsloch
Loch
Center
Nut (Nut, | ||||
Geschlüsselt | ||||
Steifigkeit
Loch
Galtel Galtel
Pfotenflut
Strukturelemente(Zahnräder, Keilnuten usw.) stellen sicher, dass das Teil seine betrieblichen Funktionen und Eigenschaften erfüllt und zu einem bestimmten Konstruktionstyp gehört.
Technologische Elementesorgen für eine einfache Herstellung des Teils (Unterstützung des Teils während der Bearbeitung) und seine Montage mit anderen Teilen (Fasen, Nuten) oder hängen mit den Herstellungsmerkmalen des Teils (Gusskehlen und -schrägen für Gussteile) und seiner Elemente (Läufe und) zusammen Hinterschnitte von Gewinden, Nuten etc. .). Technologische Elemente in Schulungszeichnungen werden manchmal nicht vereinfacht oder konventionell dargestellt oder dargestellt.
Informationselemente(Schilder, Beschriftungen, Indizes) werden normalerweise in Form von Vorsprüngen und Vertiefungen auf den Oberflächen des Teils angebracht und auf der Zeichnung genau dargestellt.
Die Form eines Teilelements hängt von den Funktionen ab, die es ausführt. Unterscheiden einfache Elemente gebildet durch eine Oberfläche und komplex, gebildet durch zwei oder mehr Oberflächen.
Technische Oberflächen bilden in der Regel Kompartimente aus zylindrischen, konischen, helixförmigen Flächen, Ebenen, Kugeln und Tori, die durch bestimmte Bilder und Dimensionen gekennzeichnet sind.
Die Elemente des Teils werden in Standardelemente mit Standardformen, -bildern und -größen (Keilnuten, Fasen, Nuten usw.) und Nichtstandardelemente (Abflachungen, Vorsprünge usw.) unterteilt.
Die geometrische Form eines Teils wird durch die Form und relative Position der es bildenden Strukturelemente bestimmt, deren Oberflächen die Gegen-, angrenzenden (Mattierungs-) und freien Oberflächen des Teils bilden.
Passende und angrenzende Flächen Kontaktdetails -
mit den Oberflächen anderer Teile verbinden und mit ihnen formen bewegliche Gelenke(Translation, Rotation, Schraube usw.) und feste Verbindungen, Sicherstellung der relativen Position und Ausrichtung der Teile sowie der Übertragung auftretender Kräfte. In diesem Fall sind die Kontaktflächen weiblich oder männlich, die angrenzenden Flächen jedoch nicht. An die Bearbeitungsgenauigkeit und Rauheit dieser Oberflächen werden erhöhte Anforderungen gestellt.
Freie Flächen Teile dürfen nicht mit den Oberflächen anderer Teile in Berührung kommen. Sie fassen alle Flächen zu einer zusammen und sorgen für deren gewünschte Lage, Ausrichtung und Kraftübertragung innerhalb des Bauteils.
Wird in Zeichnungen verwendet drei Arten von Bildern, Darstellung der Form, Position und Ausrichtung eines Teilelements: präzise
Abmessungen auf Arbeitszeichnungen müssen gemäß den Regeln von GOST 2.307-68 angewendet werden.
Die Gesamtzahl der Abmessungen in der Zeichnung sollte minimal, aber für die Herstellung und Kontrolle des Produkts ausreichend sein.
Die auf die Zeichnung angewendeten Abmessungen müssen unabhängig vom Maßstab des Bildes der tatsächlichen Größe des Teils entsprechen. Jede Größe wird einmal auf die Zeichnung angewendet.
Die Abmessungen sollten die Form des Teils bestimmen, d.h. die Form aller seiner Bestandteile und Oberflächen und ihre relative Position.
Auf jedem Bild – Ansicht, Schnitt, Schnitt, Detailelement – sind die Abmessungen genau derjenigen Elemente des Teils angegeben, für die diese Bilder erstellt wurden. Bemaßungen, die sich auf ein Element beziehen, werden im Bild so gruppiert, dass sie am besten verständlich sind.
Bemaßungen liegen nach Möglichkeit außerhalb der Kontur des Teilebildes.
Bei der Verbindung eines Teils der Ansicht mit einem Teil des Schnitts liegen die Maße für Außen- und Innenformen auf gegenüberliegenden Seiten der Symmetrieachse.
Die Flächen, aus denen die Form des Teils besteht, nehmen relativ zueinander eine bestimmte Position ein. Daher werden alle Dimensionen in Oberflächenformdimensionen und Positionsdimensionen (koordinierend) unterteilt. Die Position jeder Oberfläche wird relativ zu den Basen bestimmt. Ein Teil kann mehrere Konstruktionsgrundlagen haben (Abb. 6.1.), von denen eine als Hauptgrundlage und der Rest als Hilfsgrundlage gilt.
Reis. 6.1.
In Abb. 6.2 gibt ein Beispiel für die korrekte Anwendung von Maßen mit der Einführung einer Hilfsbasis zur leichteren Bezugnahme und Messung von Maßen. Es wird nicht empfohlen, alle Größen von einer Basis aus einzustellen. In der Regel streben sie danach, sicherzustellen, dass die Konstruktionsgrundlagen ebenso wie die technologischen Grundlagen verwendet werden. Es kann ein kombiniertes Dimensionierungssystem verwendet werden: Ein Teil der Abmessungen wird aus Konstruktionsgrundlagen ermittelt, der andere aus technologischen Grundlagen (Abb. 6.2).
Reis. 6.2.
Bemaßungsmethoden
Kettenmethode– Bemaßungen werden entlang einer Linie, in einer Kette, nacheinander aufgetragen (in Abb. 6.3. Bemaßungen A1, A2, A3, A4, A5, A6 wird die Endfläche der Welle als technologische Basis genommen). Das Verfahren zeichnet sich durch die schrittweise Anhäufung des Gesamtfehlers bei der Herstellung einzelner Elemente des Teils aus. Dies kann dazu führen, dass das hergestellte Teil unbrauchbar wird.
Koordinatenmethode – alle Maße werden von der gleichen Grundfläche aus aufgetragen (in Abb. 6.3 Maße B1, B2, B3, B4, B5, B6). Dieses Verfahren zeichnet sich durch eine hohe Präzision bei der Herstellung des Teils aus.
Kombinierte Methode – Die Bemaßung erfolgt gleichzeitig mit der Ketten- und der Koordinatenmethode. Diese Methode ist die optimalste (Abb. 6.4).
Bei der Detaillierung sollte besonderes Augenmerk auf die Abmessungen der Passflächen gelegt werden. Passmaße bestimmen die Form der Passfläche eines Teils, die Passung zur Passfläche eines anderen Teils sowie die Position dieser Flächen. Die Maße, die die Lage der Passflächen bestimmen, werden in der Regel nach Konstruktionsgrundlagen unter Berücksichtigung der Möglichkeiten der Produktprüfung festgelegt. Die Nennmaße der Passflächen und die deren Lage bestimmenden Maße müssen gleich sein. Die Oberflächen von Teilen, die nicht mit anderen Teilen in Kontakt kommen, werden als freie Oberflächen bezeichnet. Freie Bemaßungen charakterisieren die Form und Lage freier Flächen; sie werden aus Designgrundlagen übernommen. In einigen Fällen werden der Einfachheit halber Abmessungen angewendet, die bei der Bearbeitung des Teils nicht berücksichtigt werden. Sie werden als Referenz bezeichnet und sind mit dem Zeichen „*“ gekennzeichnet. In den technischen Anforderungen steht „* Abmessungen als Referenz“. Gesamtabmessungen sind die Abmessungen, die den maximalen Außenumriss eines Objekts bestimmen.
Reis. 6.3.
Reis. 6.4.
Mindestabstand zwischen Parallelen dimensionale Linien sollte ungefähr 7 mm betragen und zwischen der Abmessung und der Konturlinie - 10 mm. Beim Zeichnen von Verlängerungs- und Bemaßungslinien in der Zeichnung ist es notwendig, deren Schnittpunkte zu vermeiden. Die Verlängerungslinie sollte 3-5 mm über die Maßlinie hinausragen.
Beispiele für die Anwendung der betrachteten Regeln sind in den Arbeitszeichnungen (Anhang 3) aufgeführt.
Bei der Erstellung von Arbeitszeichnungen von Teilen, die durch Stanzen, Schmieden oder Walzen mit anschließender Bearbeitung hergestellt wurden, wird auf Teilen der Oberfläche des Teils in jeder Koordinatenrichtung, die bearbeitete Flächen mit Flächen verbindet, die keiner Bearbeitung unterliegen, nicht mehr als eine Größe angegeben (Abbildung 6.5).
Ein Teil eines Produkts erfüllt bestimmte Funktionen. Dies wird durch die geometrische Form des Teils und die physikalischen und chemischen Eigenschaften des Teilmaterials gewährleistet. Sie werden während des technologischen Prozesses der Herstellung des Teils gewonnen. In der geometrischen Form eines Teils gibt es Strukturelemente, die die Betriebsfunktionen des Teils erfüllen, und technologische Elemente, die die Herstellung des Teils gewährleisten. Strukturelemente sind grundlegend.
Zusätzlich zu den strukturellen und technologischen Elementen verfügen einige Teile über Informationselemente wie Schilder, Inschriften, Schilder usw.
Die geometrische Form eines einfachen Elements eines Teils wird durch ein Kompartiment einer Oberfläche gebildet und stimmt in vielen Fällen mit den Formen des Hauptelements überein geometrische Körper. Die Form eines komplexen Elements wird durch zwei (oder mehr) Oberflächenkompartimente gebildet. Einige Elemente, die unterschiedliche Funktionen erfüllen, können dieselbe Form und dieselben Bilder mit denselben Abmessungen in Bezug auf Form, Position und Ausrichtung haben.
In vielen Fällen werden Form, Position und Ausrichtung eines Elements in einem einzigen Bild angezeigt. In einigen Fällen ist es jedoch erforderlich, spezielle Bilder anzufertigen, um die Position und Ausrichtung des Elements zu zeigen, sowie die entsprechenden Abmessungen oder Abmessungen anzubringen in manchen Fällen nur Abweichungen von diesen Maßen.
Die Abmessungen der Position und Ausrichtung der Elemente der Teile werden von den Haupt- oder Hilfsbasen des Teils aus übernommen. Sie dienen als Hauptbestandteile Basiselement, auf denen das Teil selbst basiert, oder Hilfsgrundelemente, die als Grundlage für andere Teile dienen.
Die gewählte Größenordnung hängt eng damit zusammen zugrunde liegende Theorie, einige Elemente davon werden wir betrachten. Basierend Dies wird als Verleihen des Werkstücks oder Produkts in die erforderliche Position relativ zum ausgewählten Koordinatensystem bezeichnet. Eine Basis ist eine Fläche oder eine Kombination von Flächen, die die gleiche Funktion erfüllt, eine Achse, ein Punkt, der zu einem Werkstück oder Produkt gehört und als Unterlage dient. Beispiele für Datenbanken sind in Abb. dargestellt. 7.1, a - e, wobei 1 die Basis, 2 das Teil, 3 das Werkstück, 4 die Backen des selbstzentrierenden Schraubstocks und 5 der Zentrierkegel des Geräts ist. Die Grundflächen sind mit dicken Linien markiert. In Abb. 7.1 Die Basen sind: a und b – Flächen (Ebene und Zylinder): c und d – eine Kombination von Flächen (zwei parallele Ebenen, zwei koaxiale Zylinder); d - Achse des zylindrischen Werkstücks; e-Punkt (der Mittelpunkt des Kreises im unteren Abschnitt des zylindrischen Lochs in der Ebene des tragenden Endes). Basierend auf der Art ihrer Manifestation werden Basen in verborgene und offensichtliche Basen unterteilt. Eine verdeckte Basis ist die Basis eines Werkstücks oder Produkts in Form einer imaginären Ebene, Achse oder eines Punktes. So sind beispielsweise bei einer Halterung (siehe Abb. 5.44) die verdeckten Basen die Achse einer zylindrischen Auflagefläche mit einem Durchmesser von 50 mm und die frontale Symmetrieebene des Teils. Eine explizite Basis ist eine Basis in Form einer realen Oberfläche, die Markierungen oder Schnittpunkte von Markierungen markiert. Die offensichtliche Basis für die gleiche Halterung (siehe Abb. 5.44) ist eine tragende zylindrische Fläche mit einem Durchmesser von 50 mm.
Je nach Zweck werden gestalterische, technologische und messtechnische Grundlagen unterschieden. Eine Designbasis ist eine Grundlage zur Bestimmung der Position eines Teils oder einer Baugruppe in einem Produkt. Eine technologische Basis ist eine Basis, die dazu dient, die Position eines Werkstücks oder Produkts während des Herstellungs- oder Reparaturprozesses zu bestimmen. Die Messbasis dient zur Bestimmung der relativen Lage des Werkstücks bzw. Produkts und der Messgeräte.
Entsprechend den betrachteten Grundkonzepten werden drei Größensysteme unterschieden:
1) aus Designgrundlagen;
2) aus technologischen Grundlagen;
3) kombiniert, wobei einige der Dimensionen auf gestalterischen Grundlagen basieren, andere auf technologischen.
Das kombinierte System ist am besten geeignet, da Bemessungsgrundlagen in der Regel die Eingabe einer geringen Anzahl von Maßen (10...20 %) erfordern. Diese Abmessungen, die sich auf die Qualität des Teils und des gesamten Geräts oder der Maschine auswirken, werden mit hoher Präzision durchgeführt. Am meisten Die Abmessungen werden auf der Grundlage technologischer Grundlagen festgelegt, um eine einfache Herstellung und Messung der Teile zu gewährleisten.
Es ist zu beachten, dass in einigen Fällen die konstruktiven und technologischen Grundlagen übereinstimmen, beispielsweise die Rotationsachse bei Teilen, die durch koaxiale Rotationsflächen begrenzt sind. Eine solche Basis wird beispielsweise durch konische Mittelbuchsen an den äußersten Enden des Teils realisiert. Die Kombination von gestalterischen und technologischen sowie messtechnischen Grundlagen ist eines der wichtigen Gestaltungsprinzipien – das Prinzip der Einheit der Grundlagen.
In den oben diskutierten Teilezeichnungen für Längenmaße wird hauptsächlich das zweite Maßsystem aus technologischen Gründen verwendet.
Die Bemaßung anhand von Entwurfsgrundlagen wird weiter unten besprochen.
Bemaßungen, die die Form eines beliebigen Elements, einschließlich Löchern, bestimmen, sollten auf das Bild des Teils angewendet werden, auf dem diese Form am besten dargestellt wird. Achten Sie darauf, alle Bemaßungen an einer Stelle zu gruppieren (Abb. 7.2).
Die Abmessungen identischer Elemente sind auf der Abbildung eines davon und unter dem Regal angegeben Verlängerungslinie Geben Sie die Anzahl der Elemente an (Abb. 7.3). Die Abmessungen der Form und Position symmetrisch angeordneter Elemente (außer Löcher) können nur einmal ohne Angabe ihrer Anzahl angewendet werden (Abb. 7.4).
Maße für Fasen, Nuten für den Werkzeugaustritt, Nuten, Aussparungen und ähnliche Elemente müssen auf einem separaten Bild gezeichnet werden. Sie sollten nicht in Maßketten eingebunden werden.